Pimp My Car Battery Charger
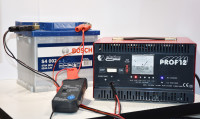
It may seem unbelievable, but in the midst of the microcontroller era, taper battery chargers are still on the market. They are basic, very robust, and charge lead-acid batteries quickly, but they have drawbacks, like an uncontrolled charging cycle, an end-of-charge current that is far too high, and they don't tolerate polarity reversals. If you own one, you can upgrade it with one of the designs presented in this article series. Here, we describe how to set up a basic protection circuit. In the second inst
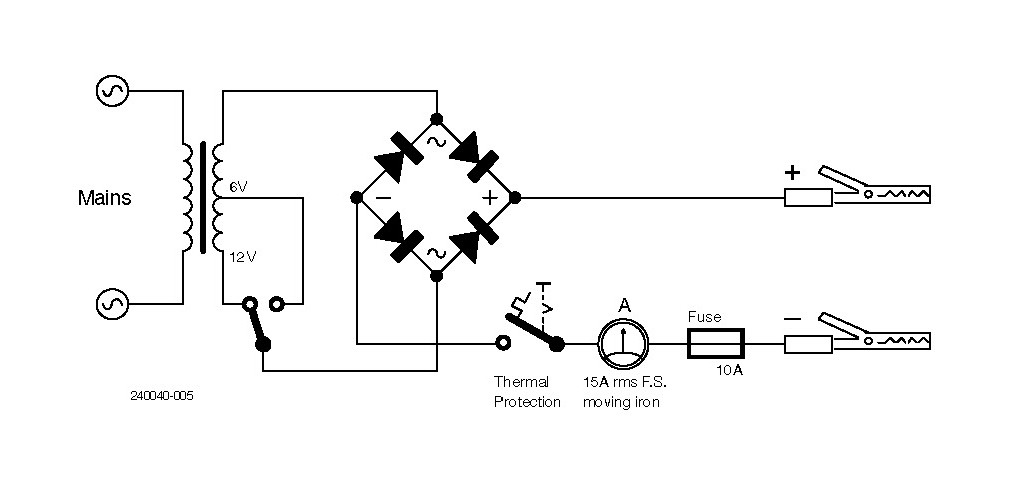
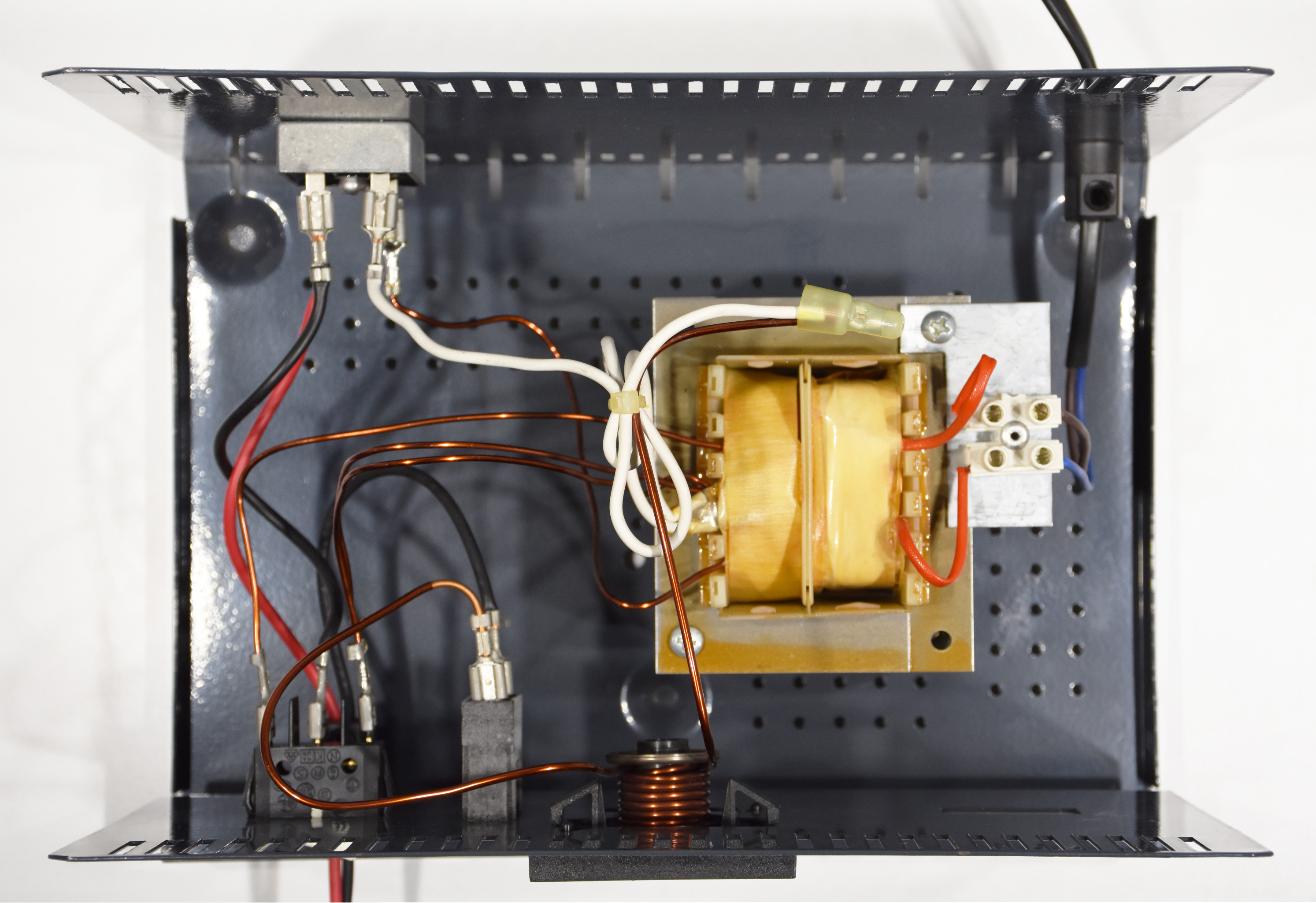
Accustomed to current, voltage and mixed-controlled regulator circuits, it seemed to me a coarsely designed product, and aware of the criticality of using it with sealed lead-acid batteries and — even worse — the new generation of AGM batteries, I was about to throw it away.
Before proceeding with our design, it could be worthy spending a few words about a standard lead-acid cell’s typical parameters. It has a nominal voltage of 2◦V, and a car battery contains a series of six of these cells. Typical constant-current charge and discharge characteristic curves of a 12◦V battery can be seen in Figure◦3.
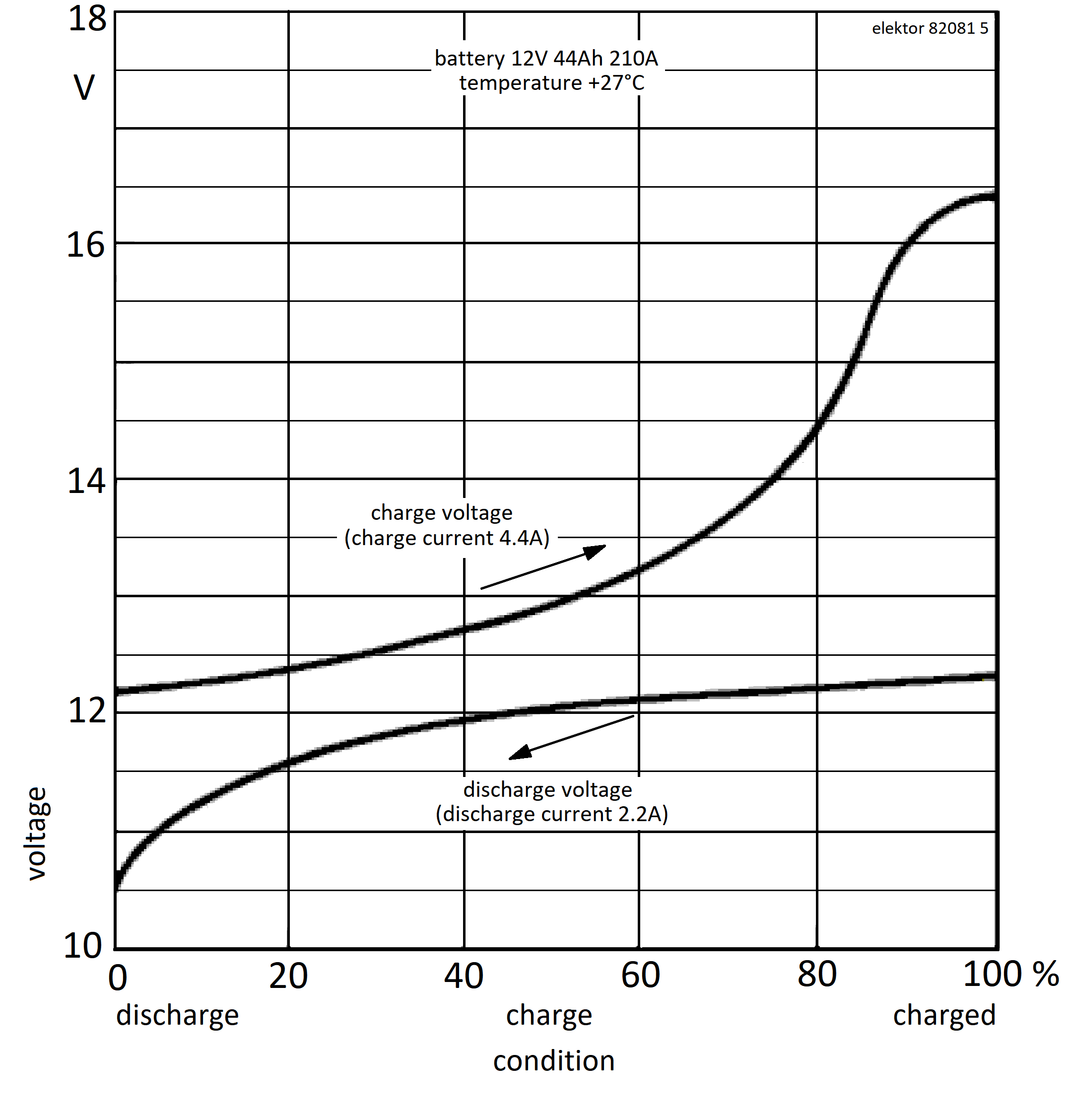
As can be seen, the curves do not go below 10.5◦V (1.75◦V per element); if the voltage is lower or, worse, goes to zero, generally the battery gets damaged and can no longer be recharged. It is good to remember that this type of battery, after assembly, is activated by filling the inside of the elements with a 30…40% solution of sulfuric acid; after activation, the voltage of each element reaches about 2.1…2.2◦V.
The first taper battery chargers date back to the ’50s and were equipped with selenium rectifiers that, later on, were replaced by silicon type. This type of charger is cheap to make and buy, it’s reliable — if used properly — but its operation is critical and is based solely on an accurate transformer design, with careful considerations about Vout(rms) and Zout, which were calculated for the specific use with lead-acid◦batteries.
We thought that to learn more about the behavior of a taper charger connected to a standard accumulator, it would be useful to make a series of accurate measurements, regardless of the modding solution we would envision. To obtain repeatable conditions for the measurements, the battery under test was connected to a 300◦W Korad◦Kel103 electronic load, which allowed to perform controlled discharge cycles to a predetermined threshold at 11.5◦V (=◦80%◦discharge).
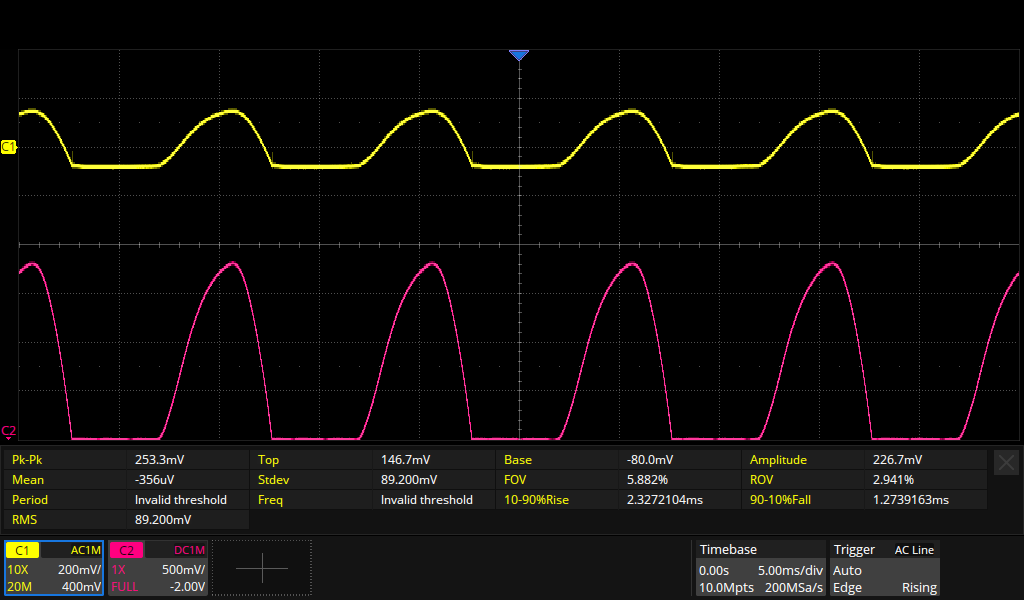
This made it possible to calculate the internal resistance value Ri of the accumulator during charging:

As can be seen, the charging current shows peaks of 10◦A, far too high to leave the device connected for long! Please note that in both Figure◦4 and Figure◦5, the baseline of the purple trace lays at the actual voltage of the battery (I◦=◦0, Vcharger◦<◦Vbattery), whilst the portions of the sine wave represent the time when Vcharger◦>◦Vbattery and the current flows.
Now the challenge was how to do it, and Walter came out with the following requisites:
- Protect the charger from accidental shorts of the clamps and from polarity reversal when connecting the battery.
- Immediate restoring of the protection in case the clamps were disconnected from the battery, without sparking.
- Add an accurate voltage check at the final stage of charging, to make the charger more usable.
- Design a cooler, microcontroller-based version, for those readers who are definitely unable to refrain from coding!
According to the requirements listed above, this first design of Walter (whose schematic is visible in Figure◦6) came out.
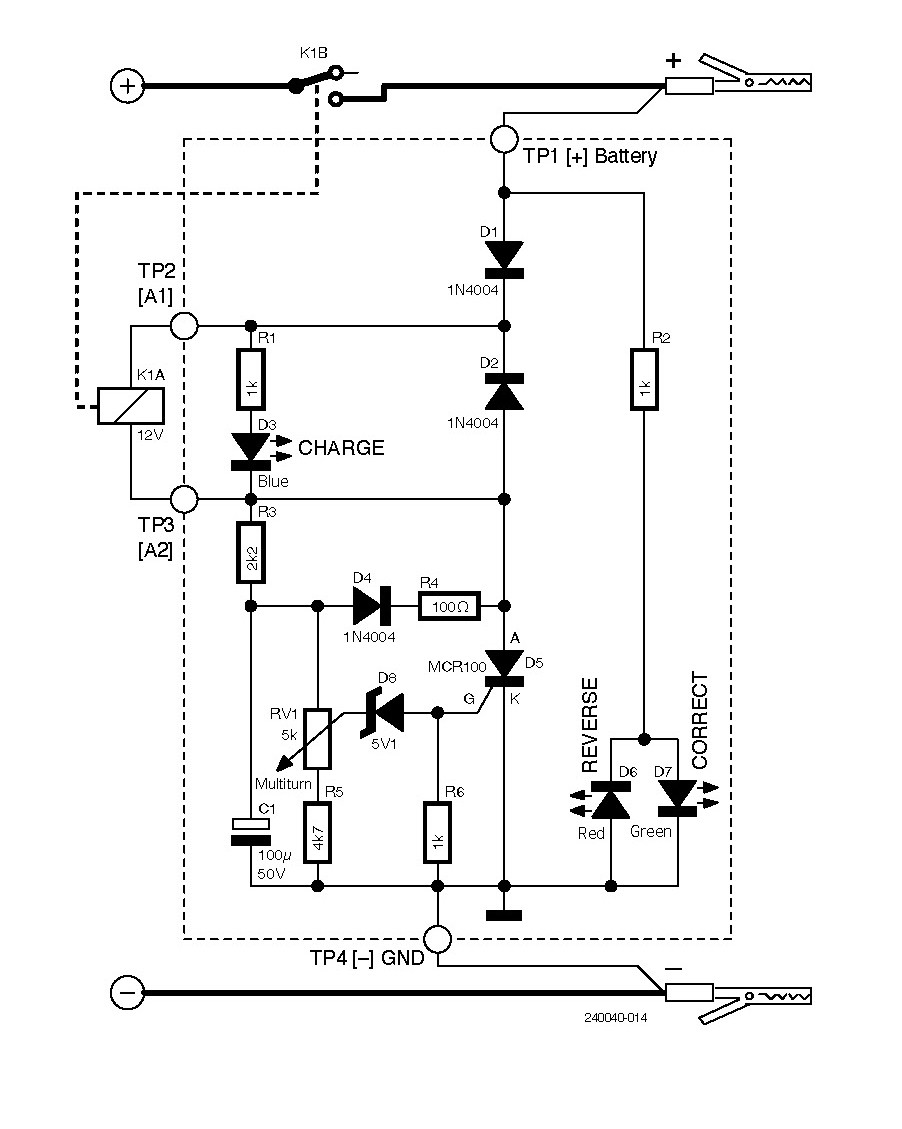
It fulfills the first two points of the requisites list, activating the relay only when the battery is connected and triggering only on a single, adjustable minimum voltage threshold. Diode D1 protects the circuit from polarity reversal of the battery clamps. The two LEDs D6 and D7 display the correct connection of these clamps: if it is ok, D7◦(green) lights up; otherwise, D6◦(red) turns on.
Calibrating the tripping voltage level is simple; turn the RV1 trimmer toward R5 and, with the charger disconnected from the mains, connect an adjustable power supply in place of the battery; set it to the desired minimum voltage, e.g., 10◦V, and adjust RV1 until the relay trips and D3 turns on. Once the SCR has started conducting, it will remain in this condition even if the battery voltage fluctuates.
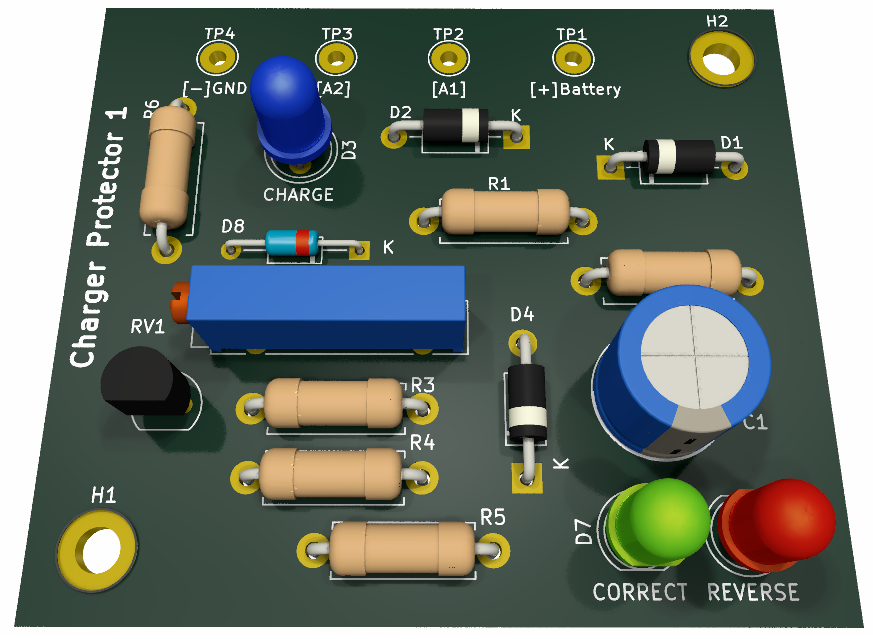
Although the addition of protection has solved the safety aspects of battery charger use, it is still not enough to ensure the good health of the accumulators being charged. Therefore, two additional designs have been developed.
This second full-analog design offers the same protection capabilities of the first design in the previous article, but adds a voltage control that stops the charging process once the target voltage has been reached. As shown in the schematic diagram of Figure◦8, this design drives the relay using a BS170◦MOSFET, rather than an SCR.
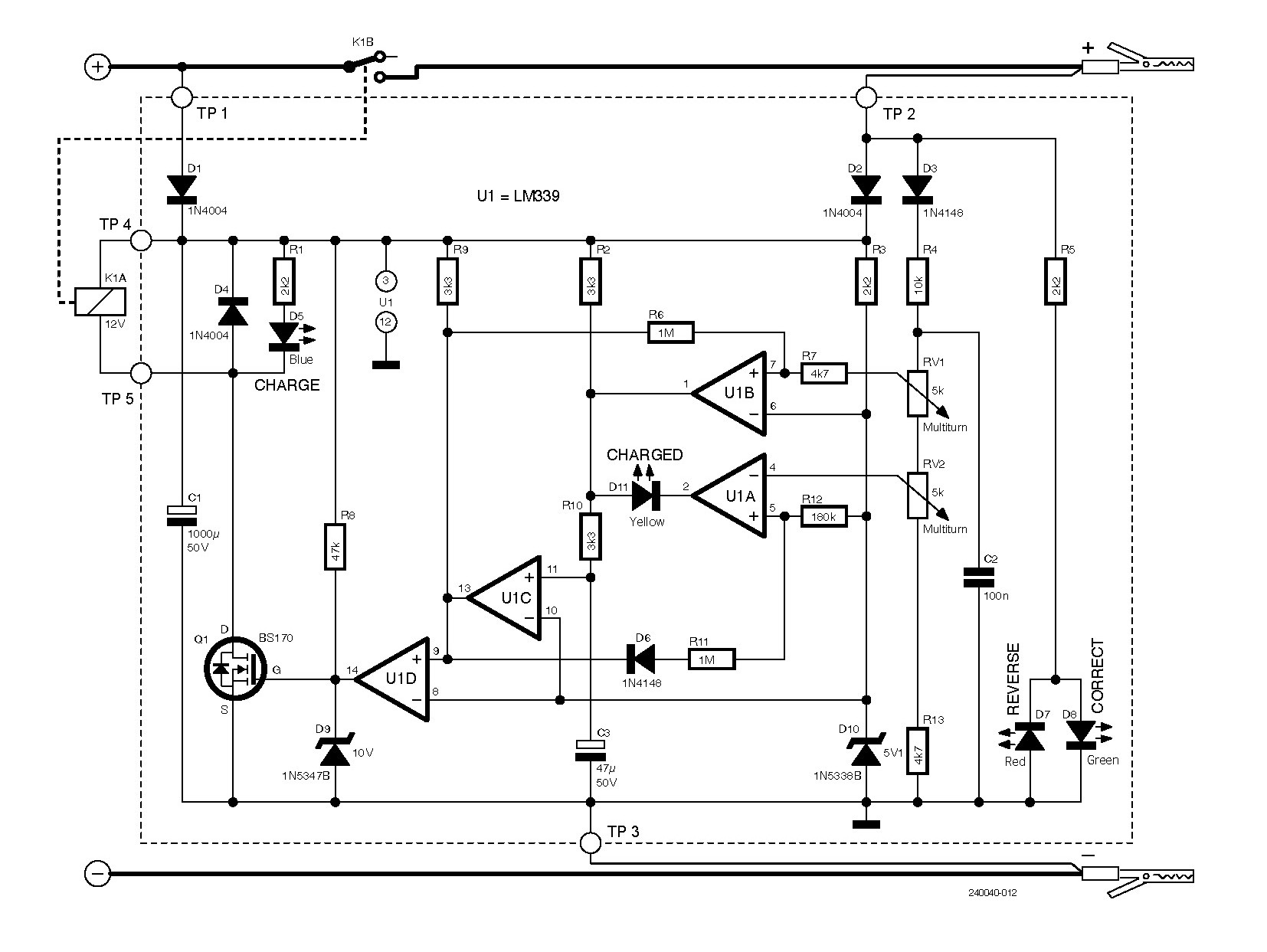
This circuit also works with both single-diode and bridge rectifier, and again it is important not to mount electrolytic capacitors upstream or downstream of the protection circuit. The schematic in Figure◦1 is also showing how to integrate this design into the circuit of the existing battery charger. Figure◦9 shows a 3D-rendering of the populated PCB.
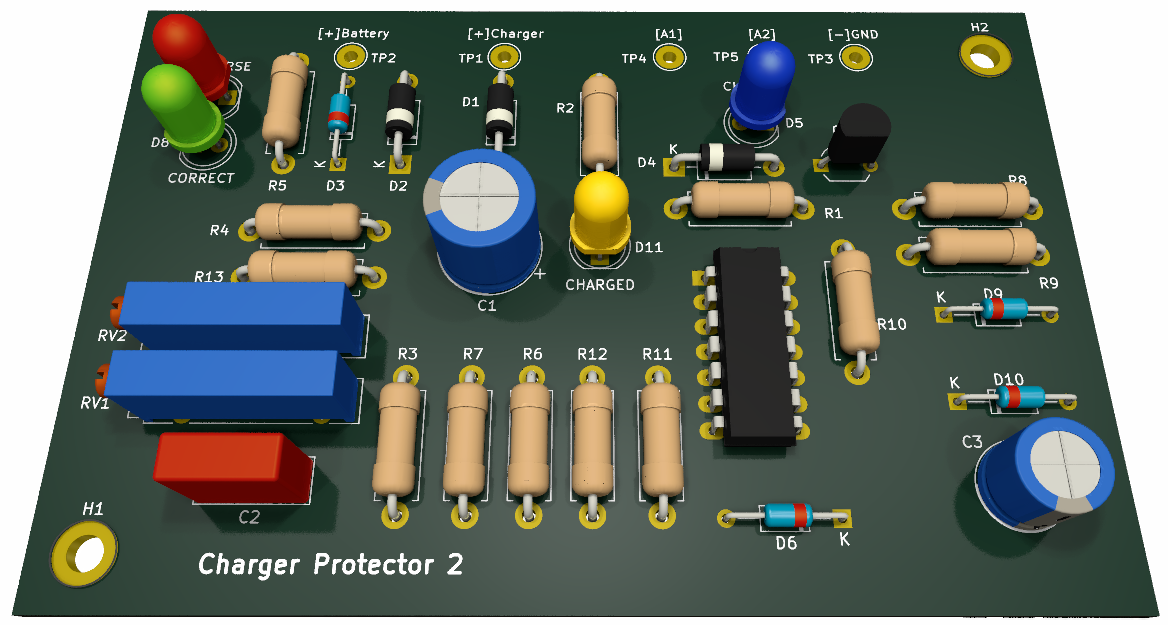
Adjustment
- Move the sliders of trimmers RV1 and RV2 toward R13.
- Power the circuit between TP2 [+] and TP3 [-] with an adjustable power supply to the desired charging voltage (e.g., 10◦V).
- Adjust RV1 until LED D5 lights up and relay K1 closes.
- Increase the voltage to the desired end-of-charge value (e.g., 14.8◦V).
- Adjust RV2 until LED D5 turns off, LED D11 turns on, and relay K1 opens.
The third and most performing circuit replicates the functionality of the second, but with set thresholds. It is built around a microcontroller, a PIC16F88 by Microchip, that measures battery voltage via a 10-bit resolution ADC◦input. The use of the microcontroller simplifies the circuit and allows the battery state of charge to be monitored with LEDs; however, it requires a 5-V voltage regulator (78L05) to power it. The schematic diagram of this third design is illustrated in Figure◦10
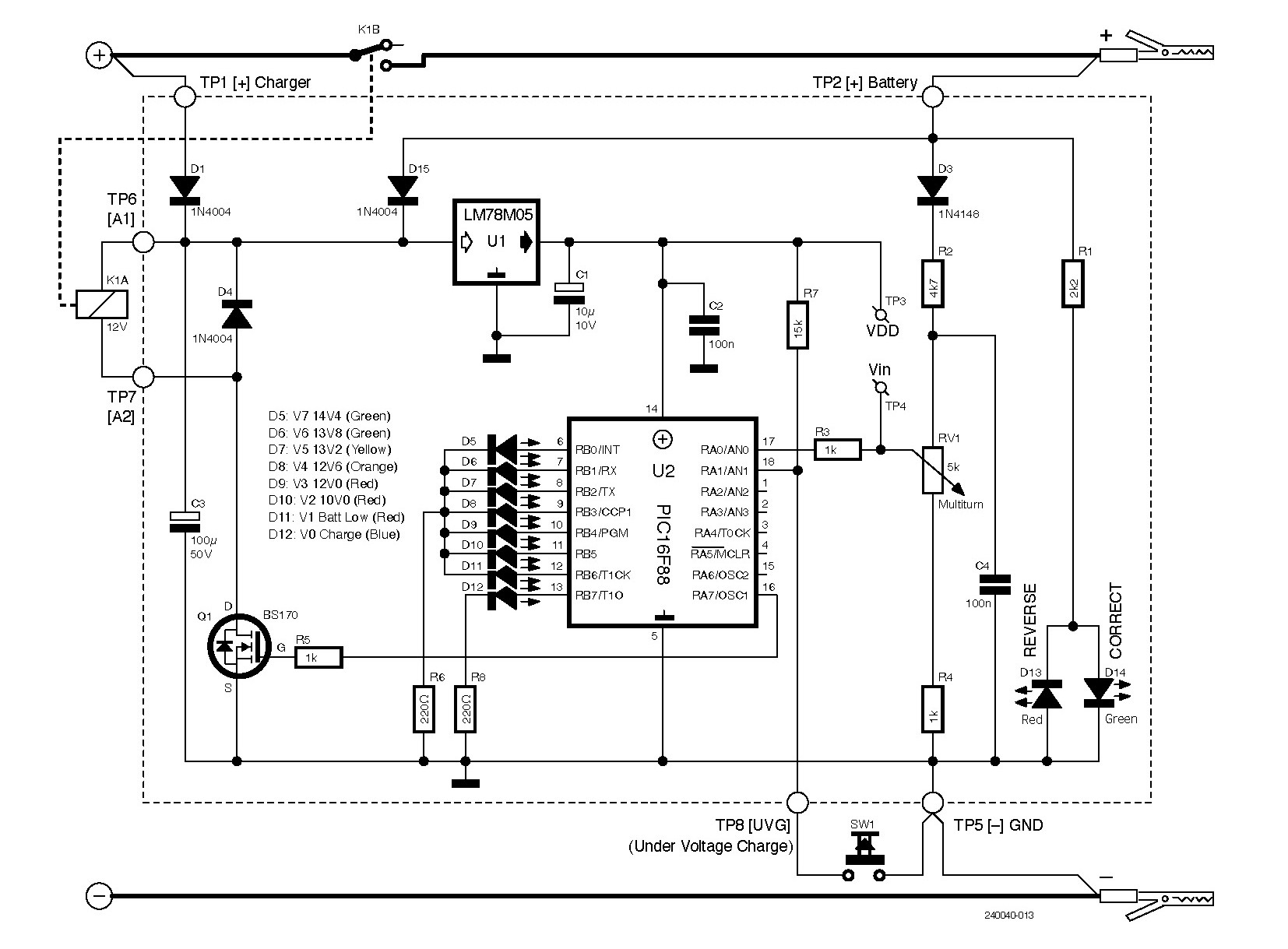
whilst its 3D rendering of the PCB is shown in Figure◦11.
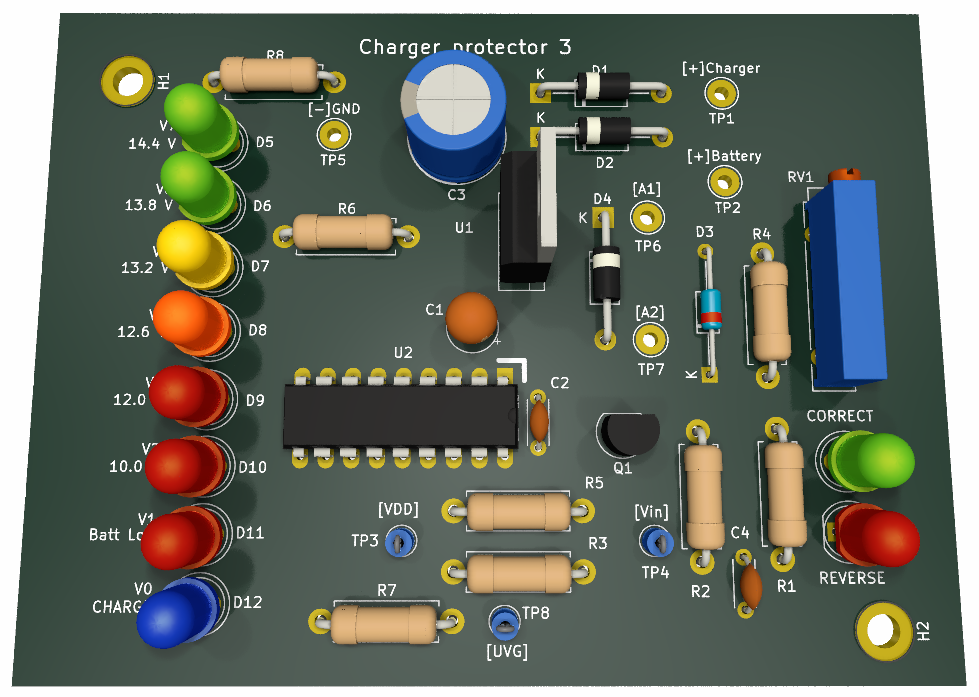
The firmware of the microcontroller is written in GCBASIC; it is part of the complete KiCad project available for download on this Elektor Labs page. Its operating diagram is illustrated in Figure◦12.
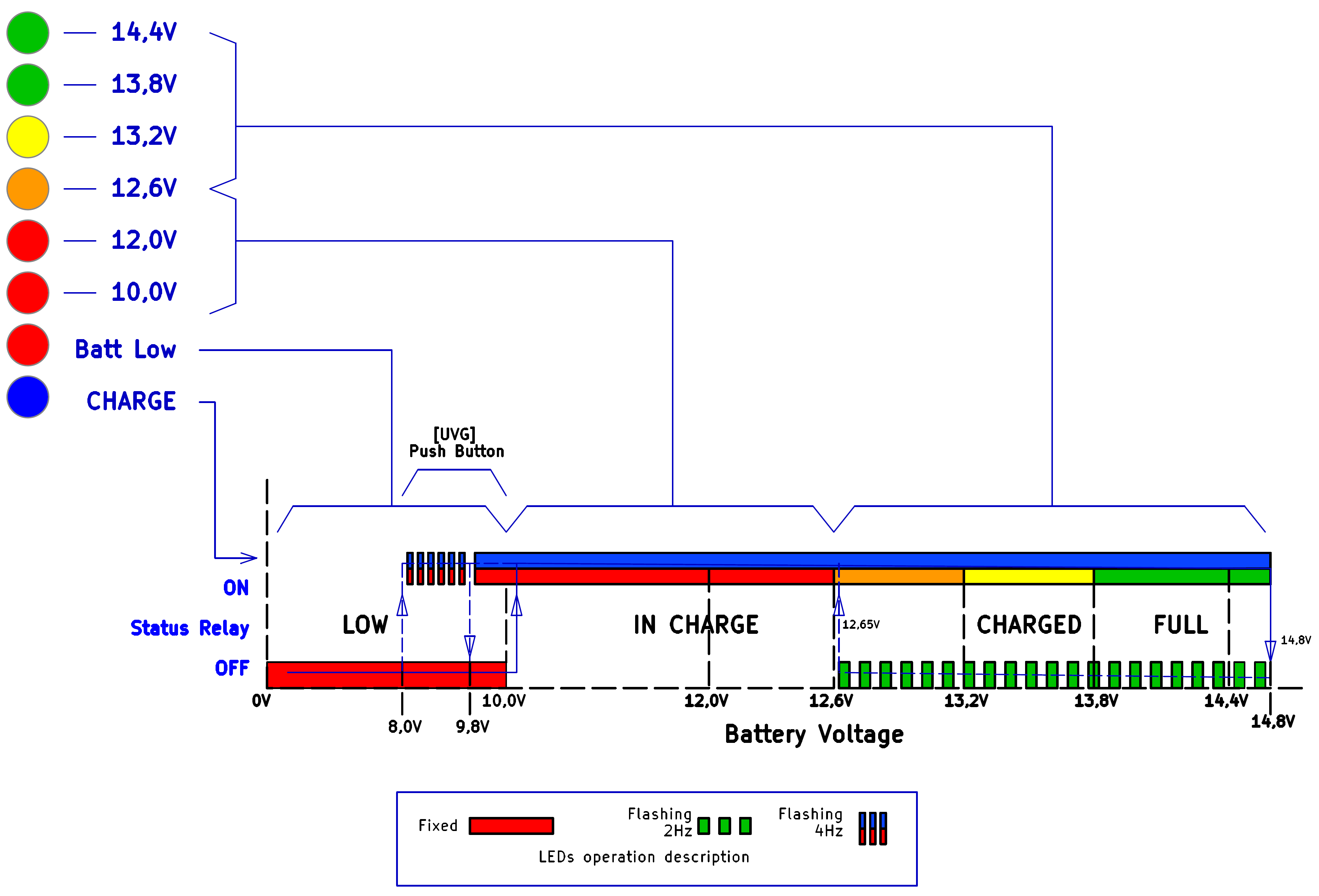
The battery voltage is measured every 10◦ms: if the conditions persist for at least 500◦ms the connection to the battery is activated by closing the control relay; as soon as a decreasing value is detected, it is deactivated, to ensure safety performance during transients.
- Activation at 10◦V, with hysteresis of 0.2◦V
- Deactivation at about 14.8◦V, with hysteresis of almost 2◦V
Up to 10◦V, LED◦D11 (V1, Batt◦Low) stays on, beyond that voltage and up to 14.8◦V the relay and LED◦D12 (V0, Charge) are activated and at the same time one of the LEDs D10…D5 is permanently lit, depending on the actual voltage measured at the battery clamps. When this voltage exceeds 14.8◦V, the relay is deactivated, the Charge LED goes off, the battery voltage starts dropping slowly and LEDs D5…D8 start flashing at a frequency of about 2◦Hz, following the voltage decrease.
Calibration
Although the thresholds are fixed, to compensate for the error due to the tolerances of the components, a calibration is required. It consists of aligning the reference voltage of the ADC, which is the VDD of the micro’s power supply, with the maximum measurable battery voltage (full◦scale), set at 15.00◦V to ensure that the thresholds are read correctly. To perform this, you need to bring the slider of trimmer◦RV1 all the way to R4, power the circuit between TP2 [+]◦Battery and TP5 [-]◦GND at 15.00◦V, adjust RV1 and simultaneously measure with a DVM 0.00◦V between TP3◦[VDD] and TP4◦[Vin]. This automatically compensates for any possible difference in the rated, theoretical 5◦V output voltage of the voltage regulator and the tolerance of the resistors values of the input divider.


As already seen in the previous article, the space inside the device was not used rationally and was not suitable for modification; therefore, as shown in Figure◦13
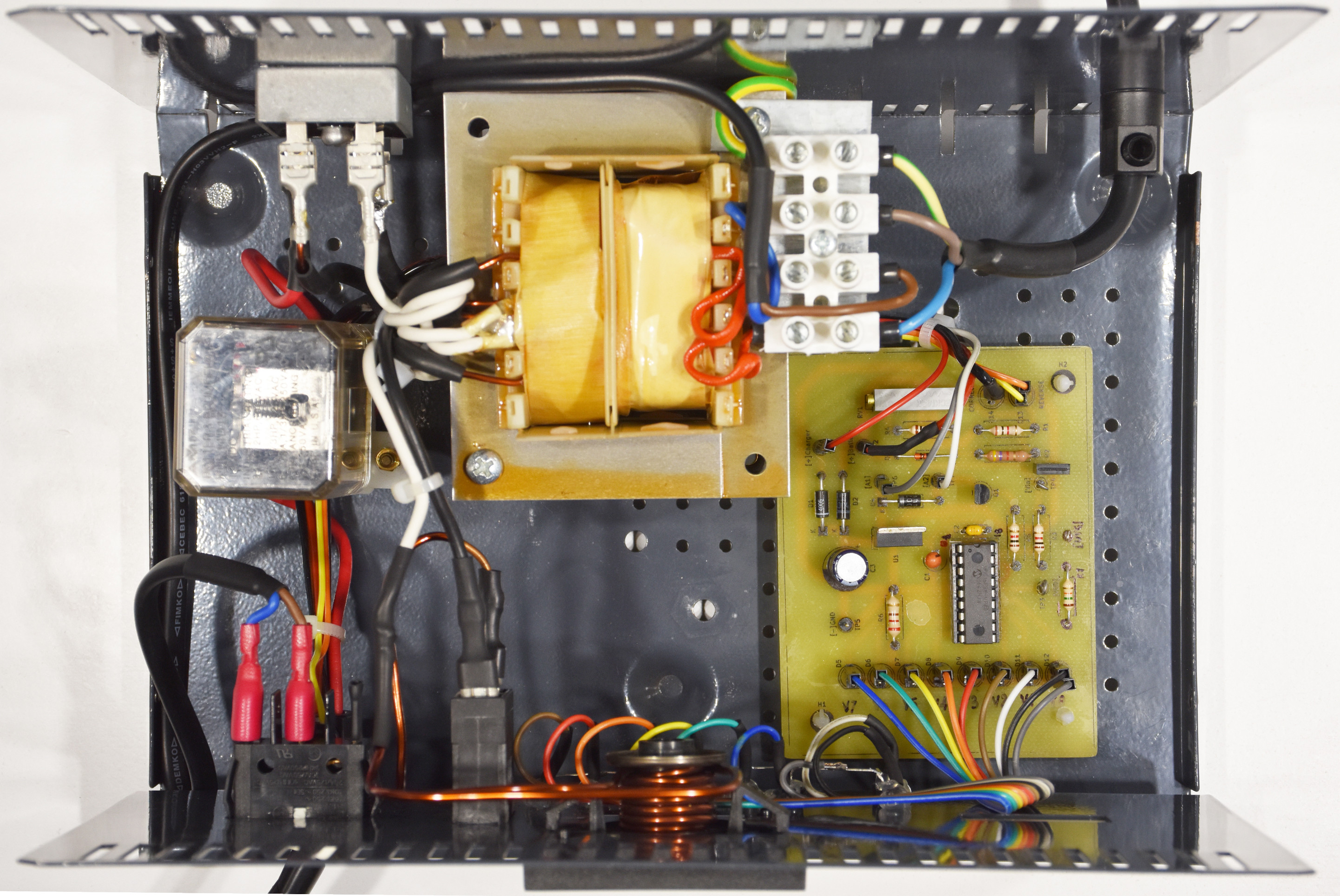
the transformer was moved to a more convenient position, then the connections to the 6◦V/12◦V switch were removed, eliminating the link to the center tap of the secondary winding of the transformer and isolating it. The original mains cable was replaced with a standard three-conductor type, and the safety ground connection to the chassis was added.
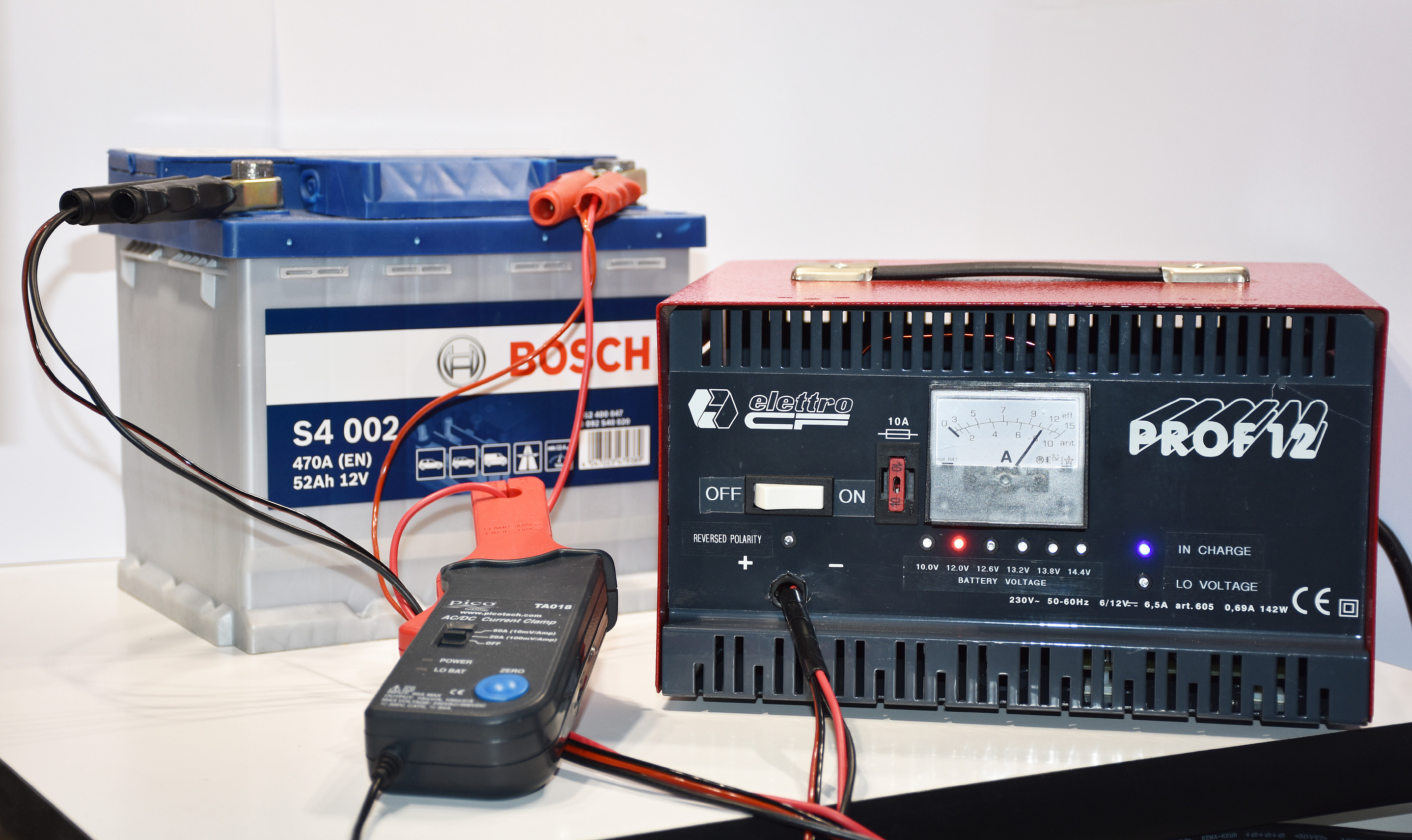
The thin red and black voltage sense wires from the battery clamps were connected to the respective inputs on the microcontroller board.
...it should be considered that a lead-acid battery emits a highly explosive mixture of hydrogen and oxygen during charging. Therefore, it is essential to comply with safety regulations and always work in a well-ventilated environment. Before connecting the clamps to the battery ends, check if your garage (or workshop) has these features. Furthermore, if you don’t know the characteristics of the electrical system of your car or motorcycle, it is always best to proceed with off-line charging (i.e., disconnecting the battery before proceeding).
------------------------------------------------------------------------------------------------------------------------------------------------------------------
Article Inserts
The Actual Charging Standards
The last-generation of (offline) Lead-Acid battery chargers are working in well-defined subsequent phases:
- Bulk Phase
- Acceptance Phase
- Float Phase
- Equalization (option)
In the Bulk Phase the first, massive part of the charging process occurs. Here, in a fully controlled charger, the current limiter is activated and the charging current reaches the set maximum value. Ideally, the initial current limit should stay between 20% and 40% of the battery capacity C. For example, the 12-V, 52-Ah battery used in our tests should be charged at a rate ranging from 10 A to a maximum of 20 A. At the end of this phase — that corresponds roughly to 75% of the overall charge — different average voltages should be considered, according to the type of the connected battery, as shown in Diagram A.
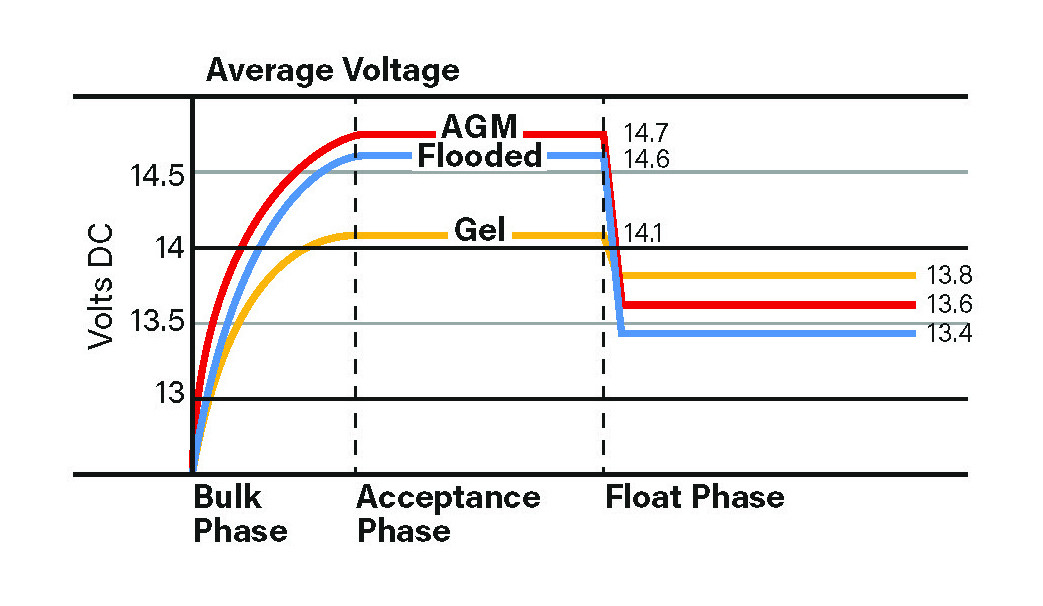
The Equalization Phase (not shown in the graph of Diagram A) is an optional one, due to its aggressive behavior to the battery. Its usage is aimed at the recovery of partially sulphated accumulators. If included in the cycle, it occurs just after the Acceptance Phase at a continuous charge rate of 4%, until the absolute maximum state of charge — and voltage — is reached. It usually stops around 15.5…16.2 V, and for this reason, it's not suitable for AGM and Gel types of lead accumulators. Even with the flooded type, however, limited to offline charging (i.e., with the battery disconnected from the system) and for a limited number of cycles, due to the wear that this process involves.
The 4-Wire Sensing
The 4-wire Sensing technique, also known as Kelvin Connection, gets its name from the English physicist who invented it in 1861.
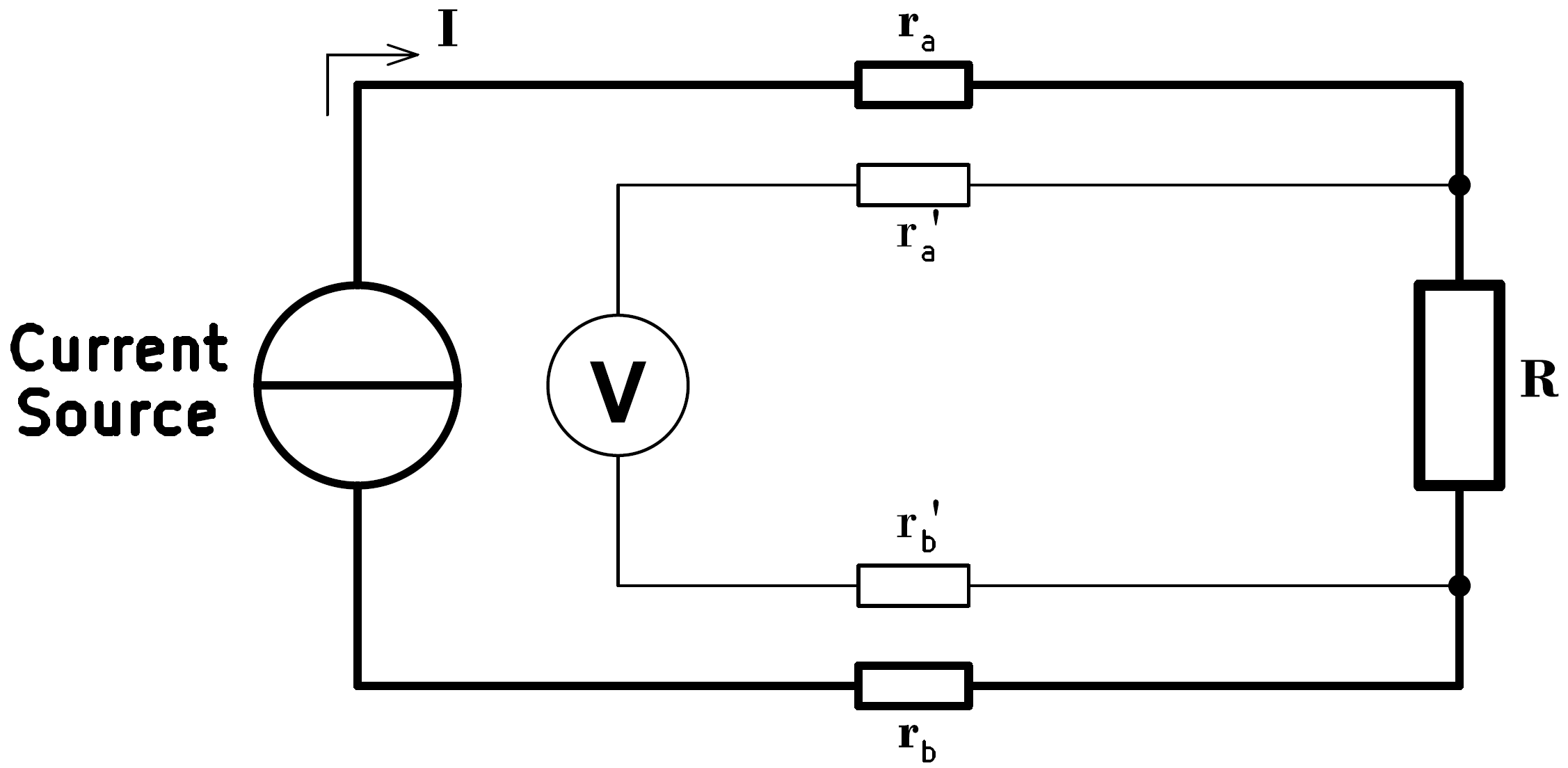
The principle on which it is based, as shown in the diagram, is to separate the load cables with internal resistance ra and rb, intended to carry the current I to the load R (a battery, in our case), from those (r'a and r'b ) designed to measure the voltage through a Hi-z sensing circuit, which follow a separate path. In this way, the voltage drop Vdrop = (I*ra+I*rb) — from the current source to the ends of the connections carrying it to R — becomes irrelevant even as the current I varies, since the voltage measurement always takes place directly at the terminals of the supplied device, often referred to as the Point of Load in industrial settings. This 4-wire connection allows to measure the value of R very accurately, even in the case of extremely low-Ohm values.
Discussion (0 commentaire(s))