Improved Radiation Meter (110538)
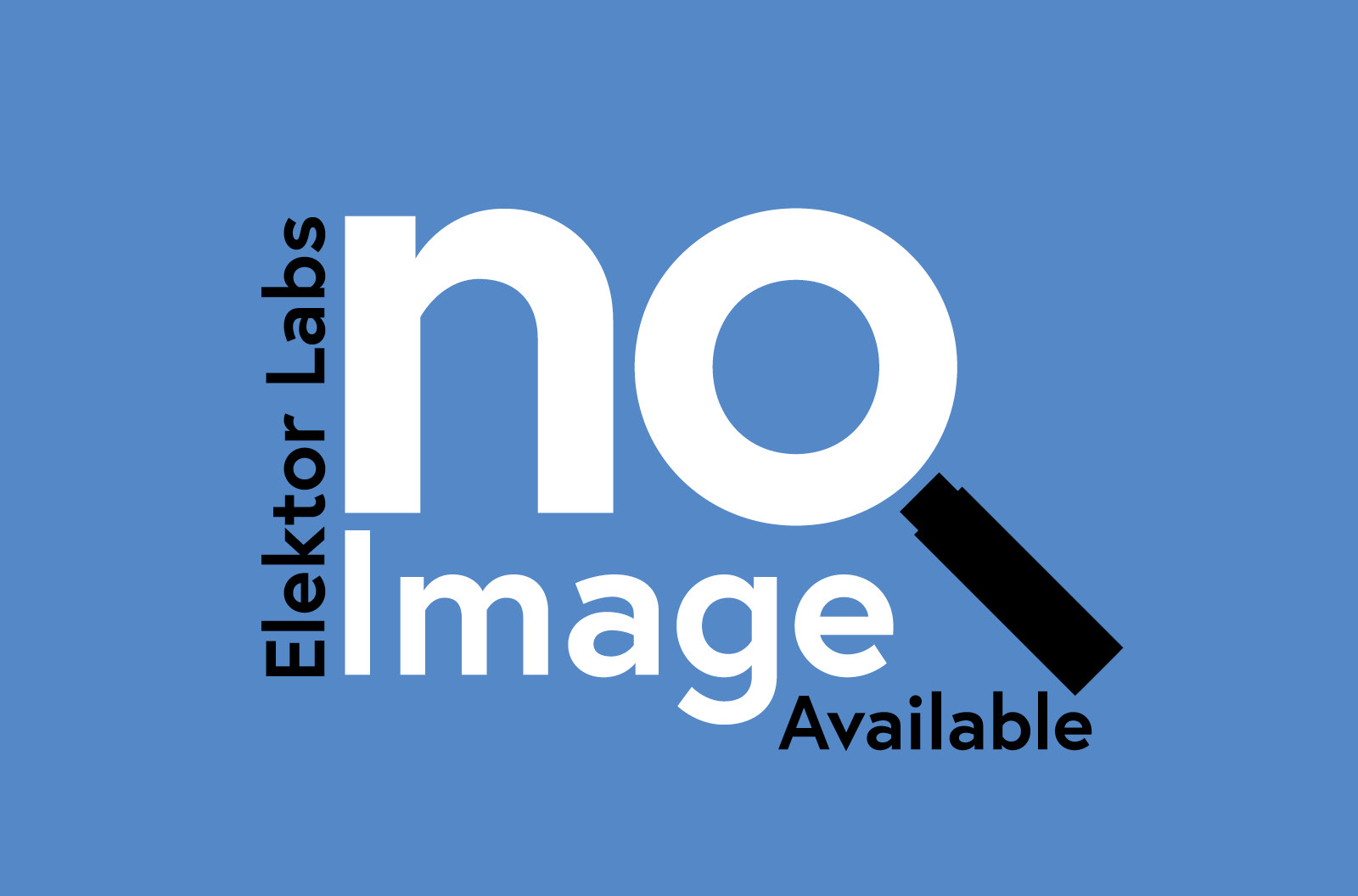
All that’s required to measure radiation is a simple PIN photodiode and a suitable preamplifier circuit. We present here an optimised preamplifier and a microcontroller-based counter. The microcontroller takes care of measuring time and pulse rate, displaying the result in counts per minute.
All that’s required to measure radiation is a simple PIN photodiode and a suitable preamplifier circuit. We present here an optimised preamplifier and a microcontroller-based counter. The microcontroller takes care of measuring time and pulse rate, displaying the result in counts per minute.
Published in issue 419, November 2011
PCB, bare, 110538-1
Programmed controller ATmega88PA-PU, 110538-41
Kit of parts incl. display and programmed controller, 110538-71
Counter for alpha, beta and gamma radiation
By Burkhard Kainka
The device we describe can be used with different sensors to measure gamma and alpha radiation. It is particularly suitable for long-term measurements and for examining weakly radioactive samples. The photodiode has a smaller sensitive area than a Geiger-Müller tube and so has a lower background count rate, which in turn means that the radiation from a small sample is easier to detect against the background.
A further advantage of a semiconductor sensor is that is offers the possibility of measuring the energy of each particle, allowing a more detailed investigation of the characteristics of a sample. The optional PC-based software displays the energy spectrum, permitting a very detailed analysis to be carried out.
Preamplifier
In the June 2011 issue of Elektor we described experiments using a BPW34 photodiode as a detector for gamma radiation [1]. Only simple experiments could be carried out as the pulses from the detector are very short. Here we look at an improved preamplifier design, which avoids the use of a comparator, and which generates output pulses that can be heard directly or processed further. The amplifier uses a BF245B JFET at its input followed by an opamp circuit, providing an overall voltage gain of 30 000. At the output it delivers pulses with an amplitude of up to 200 mV with a pulse width of around 0.5 ms, which can be rendered audible without further processing or which can be used to drive a counter.
The circuit (see Figure 1) can use several photodiodes in parallel at its input. On the one hand, this increases the pulse rate; unfortunately, this advantage is on the other hand offset by the reduced amplitude of the sensor’s output due to its increased total capacitance.
The JFET input offers good signal-to-noise ratio and a high input impedance. A DC level of about 2 V or 3 V appears across the BF245B’s source resistor, more or less independent of the supply voltage. If a BF245C is used, this voltage will be higher; in the case of a BF245A, lower. This voltage level is a suitable operating point for the opamp. The capacitance of the photodiode drops as the voltage across it increases, and so it is operated at the full supply voltage, with the gate of the JFET being pulled to ground through a 20 MΩ resistance.
The counter
The pulse counter is constructed using an ATmega88 and a two-line LCD. The power supply voltage of 9 V to 12 V is taken via D1 (for reverse polarity protection) to voltage regulator IC2, a 78L05, which generates the 5 V supply for the microcontroller and the sensor circuit. There is an ISP connector on the board to make software updates easy and there is a further connector to which a serial interface can be attached to allow transfer of data and settings to and from the PC. The RXD and TXD signals on this connector are at TTL levels and compatible with the FT232R USB serial bridge breakout board (‘BOB’) published in the September 2011 issue of Elektor.
The sensor amplifier is attached at connector K1. Its output signal, which is superimposed on a quiescent DC level, is taken directly to the ADC0 analogue input of the microcontroller. At start-up the microcontroller determines the quiescent DC level and any incoming pulses that exceed this level by at least a preset amount are counted. Button S1 starts a new measurement without resetting the stored quiescent level: this lets you first set the quiescent level with the sensor not pointing at the sample of interest, and then start the measurement proper with the sensor in position.
Any pulse that is counted also results in a visible indication on LED1 and on output K5, where a small loudspeaker can be connected for an audible indication. Any loudspeaker with an impedance of between 8 Ω and 32 Ω can be used, although it is a good idea to wire it in series with a volume control (a 1 kΩ potentiometer with a logarithmic taper) in case after a while the ticking sound starts to get annoying.
The unprocessed signal is also taken to connector K4 via C8. This can be wired to a BNC socket for to allow, for example, connection of an oscilloscope. Alternatively, an audio amplifier can be connected, in which case particles of different energies will be distinguishable by their sounds.
Printed circuit board
The printed circuit board for the project (Figure 2) comes in two sections. The sensor board can be separated from the main part and connected using a three-core cable. This allows the sensor to be mounted more easily in a light-tight enclosure.
The LCD and pushbutton are mounted on the reverse of the board; all other components are mounted on the top side. Sensor D1 can be mounted on whichever side of the board is more convenient, bearing in mind how the unit will subsequently be mounted in its enclosure.
The circuit is best tested first without the sensor diode fitted. The output of the opamp circuit should be a mid-level DC voltage, and the input should be so sensitive that even moving a finger near it will trigger the counter.
The sensor can now be mounted: Figure 3 shows it mounted on the reverse of the board. The sensitive area of the device is then under the lower right side of the board. It is important to ensure that the BPW34 photodiode is fully shielded from incident light and that the circuit area around the diode is carefully screened. During construction fit a small piece of black insulating tape under the photodiode: this will block light that might otherwise pass through the not-quite-opaque printed circuit board. Figure 4 shows the component side of the populated prototype board.
Aluminium foil can be used to screen the area around the photodiode, on both sides of the board: see Figure 5. The foil should be connected to ground. This will give good shielding against both light and interference that could otherwise lead to false counts. Further pieces of insulating tape can be used under the aluminium foil to prevent shorts to the rest of the circuit. The foil should be fitted tightly over the photodiode, as otherwise it is possible accidentally to construct a condenser microphone, with the counter responding to loud noises! The connection to the foil can be made, for example, using a bolt with two washers.
We can now test the operation of the board with the photodiode in its light-tight enclosure. A DC level of about 2 V to 3 V should appear at its output. This serves to check that there is indeed no light falling on the photodiode: if the operating point of the circuit is too high, this means that some light is probably getting in. When everything appears to be working satisfactorily, it should be possible to use an oscilloscope to observe background noise with an amplitude of around 5 mVpp.
The unit can now be tested with a radioactive sample. Place a sample, for example of a suitable mineral, directly in front of the sensor. Any gamma radiation emitted by the sample will give rise to pulses clearly visible above the background noise level. Each pulse whose amplitude exceeds a certain level will be counted. The threshold level can be adjusted later in the software. If you do not have a suitable sample to hand, all you need to do is wait: after a few minutes at the most a cosmic ray will impinge on the sensor and be counted (see Figure 6, Figure 7 and Figure 8).
Alpha particles
The BPW34 comes in a plastic package which is too thick to allow alpha particles through. However, we can replace the BPW34 with a BPX61, with the glass window removed. The photodiode itself is now completely exposed and alpha particles can now be detected, resulting in signals with an amplitude some ten times greater than those produced by gamma rays. The same sensor amplifier can be used, but it must now be separated from the counter board and mounted in its own light-tight screened box. The sample to be examined must be placed inside the box next to the sensor, as even one layer of aluminium foil is thick enough to impede alpha particles (see Figure 9 and Figure 10).
A small abrasive disc mounted in a hobby drill can be used to remove the glass window from the BPX61. The job has to be done extremely carefully as any damage to the diode itself or to its bonding wires spells doom for the device.
A lidded tin makes a good screened enclosure. The metal must be connected to signal ground so that it provides electrical shielding as well as screening from ambient light. The lid must of course be fitted before any readings can be taken.
The oscilloscope shows high-amplitude peaks, up to 2 V, corresponding to alpha particles. Smaller peaks can also be seen: the BPX61 is, like the BPW34, sensitive to gamma rays too. Hence we can discriminate between the two types of radiation on the basis of the pulse amplitude.
Firmware
The firmware is available for free download at [2]. It is written in BASCOM-AVR and is reasonably easy to understand. The output voltage from the preamplifier in the quiescent state is about 2 V, on top of which we see the sensor pulses. In order to count these pulses we need to use some kind of comparator, and the ATmega is fast enough to do this job in software. At start-up the unit computes an average background signal level by averaging 1000 readings (see Listing 1). The averaged value U is then increased by a trigger threshold increment L to produce a threshold U0 which gives adequate margin over background noise for reliable counting.
Listing 1: Averaging readings and setting the trigger threshold
Readeeprom L , 1
If L = 255 Then L = 10
U = 0
For N = 1 To 1000
D = Getadc(0)
U = U + D
Next N
U = U / 1000
Um = U
U0 = Um + L
N = 0
During the measurement itself (Listing 2) the output of the software comparator is also used to drive digital output ports PortB.0 and PortB.1. An LED is connected to pin B.0 to give a brief flash of light for every pulse detected. An small loudspeaker can be connected to B.1 with a resistor or a volume control potentiometer in series.
Listing 2: Detecting a pulse
Do
Max = U0
Do
D = Getadc(0)
Loop Until D > U0
Portb.0 = 1
Portb.1 = 1
If D > Max Then Max = D
Do
D = Getadc(0)
If D > Max Then Max = D
Loop Until D < U0
N = N + 1
Max = Max - Um
If Max > 255 Then Max = 255
Print Chr(max);
Portb.0 = 0
Portb.1 = 0
Loop
The maximum level achieved by each pulse is also measured and output as a single byte over the serial interface, to which a PC can be connected. This single-byte format is chosen so that no extra time is wasted in data transmission. As a consequence the maximum pulse height that can be reported is 1.25 V, which corresponds to a byte value of 255. Pulses of greater amplitude than this are clipped to the maximum value.
The display continuously shows the current counter value, updated once per second (Listing 3). Accompanying this on the lower line of the display is the total time elapsed since the beginning of the measurement, shown in minutes and seconds. At the end of each full minute the program calculates the count rate in pulses per minute.
Listing 3: Timer processing and LCD output
Tim1_isr:
Timer1 = -7812
S = S + 1
If S = 60 Then
S = 0
M = M + 1
Count = N
Count = Count / M
Locate 2 , 10
Lcd Count
Lcd " "
End If
Locate 1 , 10
Lcd N
Locate 2 , 1
Lcd M
Lcd ":"
Lcd S
Lcd " "
The sensitivity of the unit depends chiefly on the threshold setting for the comparator. This is initially set at ten A/D conversion steps above the quiescent level, but the value can be modified if desired using the serial interface. A threshold of three steps has proved a good compromise, giving reliable pulse counting while still being above the background noise level. To change the threshold simply send a single byte to the unit over the serial port. Values of up to 100 are used immediately as the new threshold value. If you wish to store the new threshold as the default value in the microcontroller’s EEPROM, add 100 to the value before sending it. In this case the new setting does not take immediate effect. So, for example, sending the byte value 103 will set the threshold after the next reset to three.
PC software
The Visual Basic program AlphaGamma (available for free download at [2]) receives incoming bytes over the serial port and counts them in 255 bins. After a while collecting these values it becomes apparent which energy levels are particularly common in the incident radiation. The energy spectrum is plotted in a simple graph (Figure 11). The higher energy values are due to alpha particles: because of the relatively thick sample used these tend to lose a lot of their energy on their way to the sensor, and so no sharp energy lines are seen with this sample. When looking only at gamma rays using the BPW34 the higher energy levels are empty; when alpha particles are detected they usually have an energy beyond the range of the display, which accounts for the sharp peak seen at the maximum energy value.
Listing 4 shows the main timer routine. In this routine all the bytes found in the input buffer are read in and processed. For each byte one element of the array ‘bin’ is incremented and then the results are displayed graphically.
Listing 4: Processing the received energy values
Private Sub Timer1_Timer()
While INBUFFER() > 0
d = READBYTE()
bin(d) = bin(d) + 1
Wend
For n = 1 To 255
x1 = 2 * n
x2 = 2 * n + 2
y1 = 200 - bin(n)
y2 = 200 - bin(n + 1)
If y1 > 255 Then y1 = 255
If y2 > 255 Then y2 = 255
Picture1.Line (x1, y1)-(x2, y2)
Next n
End Sub
The program also allows the trigger threshold to be set to any value from 2 to 100. The value can be used immediately or stored in EEPROM (Listing 5).
Listing 5: Setting the trigger threshold
Private Sub Command2_Click()
l = HScroll1.Value
SENDBYTE l
End Sub
Private Sub Command4_Click()
l = 100 + HScroll1.Value
SENDBYTE l
End Sub
Alpha particles can easily be filtered out, for example by placing a piece of aluminium foil in front of the ‘naked’ BPX61. Doing this considerably reduces the energy spectrum obtained from a sample of pitchblende (Figure 12).
Beta particles also produce measurable signals. The pulse amplitude they produce is generally similar to that which results from gamma radiation, and it is therefore difficult to distinguish between the two. To test for beta particle sensitivity it is possible to take readings over a long period using the BPX61 and a small sample of potassium chloride. Ordinary potassium chloride contains a small percentage of radioactive potassium-40. Some 90 % of the disintegrations produce beta particles with energies of up to 1.3 MeV; the other 10 % produce gamma quanta with energies of 1.5 MeV. The beta spectrum shows a characteristic falling-off in energy up to a clearly-visible maximum value, while the gamma spectrum takes the form of a sharp line. The result is the full spectrum shown in Figure 13, demonstrating that the photodiode is capable of detecting alpha, beta and gamma radiation.
Internet Links
[1] www.elektor.com/110372
[2] www.elektor.com/110538
Published in issue 419, November 2011
PCB, bare, 110538-1
Programmed controller ATmega88PA-PU, 110538-41
Kit of parts incl. display and programmed controller, 110538-71
Discussion (3 commentaire(s))